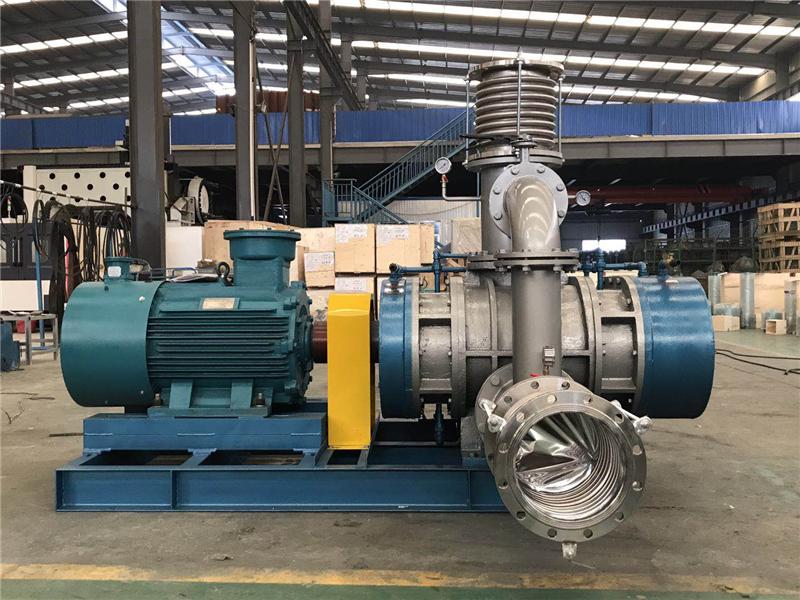
1、MVR principle
MVR is a mechanical vapor recompression (MVR) technology. Recompression is the use of secondary steam and its energy produced by the evaporation system itself to transform low grade The steam of the compressor is upgraded by the mechanical work of the compressor to a high-grade steam heat source. This cycle provides heat energy to the evaporation system, thereby reducing the demand for outside energy as an energy-saving technology.
In order to make the manufacture of the evaporation device as simple as possible and easy to operate, centrifugal compressor and Roots type compressor can be used. These machines in 1:1.2 to 1:2 compression ratio in the range of its volume flow is high.
2, mechanical vapor recompression evaporator (MVR evaporator)
The process is that the steam at low temperature is compressed by the compressor, the temperature and pressure increase, the enthalpy increases, and then enters the heat exchanger to condense, so that the steam can be transferred to the heat exchanger. Make full use of latent heat of steam. Except for start-up, no steam is generated during the entire evaporation process.
As shown in the figure, the secondary steam generated in the evaporation process will be compressed, and then returned to the evaporator as heating steam.
The evaporation of secondary steam is low temperature, but contains a lot of latent heat, the second steam compressed by the compressor to increase the temperature (pressure). The heat exchanger returned to the original evaporator is used as a heat source to maintain the boiling state of the feed liquid, while the heating steam itself condenses into water. In this way, the original steam to be discarded will be fully utilized, latent heat recovery, improve thermal efficiency, the economy is equivalent to the multi-effect evaporation of 20%. Effect.
-MVR Evaporator Key Features.
1) No raw steam required
2)Low energy consumption and low operating costs
(3) It can be combined with a crystallizer to make a continuous crystallizer of MVR type.
Comparison of the cost per ton of water evaporated by MVR evaporators versus multi-effect evaporators.
In order to reduce operating costs, this program uses MVR technology, which uses imported fans to compress the secondary steam to reach the system Evaporation temperature difference required for operation. Except for the use of steam to preheat the system when it is turned on, the complete system requires only electricity for normal operation and no additional raw steam. The suction side of the fan is partially vacuumed, which reduces the flash vapors formed when the slurry enters the centrifuge. No additional raw steam is required for the operation of the system, since all the high temperature condensate produced by the system is used to preheat the material to near boiling point. The heat energy generated by the fan compressing the steam will be used to preheat the remaining material and compensate for the heat loss generated by the system, providing adequate Heat ensures the exhaustion of air and non-condensable vapor.
The fan is driven by a variable frequency control motor. The variable frequency control allows the fan to run at the optimum speed, eliminating the loss of inlet guide vanes and reducing the impact on the whole system by soft starting. and extend the service life of fans and motors. When it is necessary to operate below the design capacity of the system, the economic operation of the system can be ensured by adjusting the inverter.
How do I choose the most critical part of the MVR evaporator system?
With the further improvement of environmental protection and energy saving requirements, MVR evaporators are becoming increasingly popular, including wastewater concentration treatment, with very low operating costs. Within the evaporation unit of choice. The domestic mechanical vapor compressor industry has been booming in the last two years and the share of domestic compressors has been increasing. So, how to choose the most critical steam compressor in the MVR evaporator?
Steam compressor is a heat recovery system for the steam generated by compression and steam temperature and pressure to increase the key equipment. The role is to low pressure (or low temperature) of the steam pressure heating, in order to achieve the process or the required temperature and pressure requirements of the project.
Mechanical steam compressor is divided into Roots steam compressor and centrifugal steam compressor fan two kinds, while the centrifugal steam compressor fan is divided into ordinary Centrifugal compression fans and single stage high speed centrifugal steam compressors. Different fan types have different characteristics and have their own advantages in different application conditions.
The figure below shows the temperature rise – flow rate relationship for Roots compressors, high-speed centrifugal compressors and centrifugal blowers.
(1) Roots Steam Compressor Fan
Roots compressor is a positive displacement fan, compared to ordinary centrifugal compressors, high compression ratio, single-stage compression temperature rise of up to 25 degrees Celsius.
For Roots steam compressor, it has better stability due to its lower rotational speed.
In general, the rotational speed of Roots steam compressor is 980-1450r/min, while the rotational speed of ordinary centrifugal steam compressor is In 6000 to 9000r/min, and the maximum speed of single-stage high-pressure centrifuge can reach 30,000r/min.
Of course, for Roots fan, its disadvantage is also obvious, its single-stage volume flow rate is too small, low efficiency, short maintenance cycle (generally). (2000h/time) is its inherent defect; at the same time, the noise spectrum of Roots fan is wide, and the low and medium frequency of 63-8000Hz is the most important. Noise as the main component, the noise in operation up to 100 decibels or more, on personnel health injuries.
(2) Ordinary centrifugal steam compressor
General centrifugal steam compressor compression temperature rise of 8 to 10 degrees Celsius, the current main application of basic models for the import of compressors, the advantages of is high efficiency and stable performance.
Two centrifugal steam compressors can be connected in series for higher compression ratios where a higher compression temperature rise is required, but at the same time, the fan is not as efficient as it should be. The efficiency will be reduced.
Usually there is a boiling rise during the evaporation process, and some solutions can boil even very high, which requires two stages or Three-stage fan used in series.
(3) Single-stage high-speed centrifugal compressor
Single-stage high-speed centrifugal compressor is characterized by high fan speed, a high compression ratio, and thus a high compression temperature rise, up to 25 to 30 degrees Celsius, it also has high efficiency, low energy consumption, larger processing capacity, and thus a wider range of applications.
MVR Technology Development Status
In the 1970s, as the demand for energy increased and the price of energy skyrocketed, MVR technology became increasingly popular. Researcher’s attention and research, and successfully applied to the operation of evaporation.
In 1957, the German GEA company for evaporation separation operation process of high energy consumption problems, developed a commercial MVR evaporation system. In practice, the MVR technology developed by GEA has shown that it consumes 16.4 kWh/t for tanker truck cleaning industrial wastewater concentration, 9.8 kW-h/t for concentration of various types of dairy and whey products, and 16.4 kWh/t for the treatment of wheat starch. kWh/t; 9.8 kW-h/t for the concentration of all types of dairy and whey products; 16.4 kW-h/t for the treatment of wheat starch; 9.8 kW-h/t for the concentration of all types of dairy and whey products. In 1999, General Electric started to use MVR in heavy oil extraction wastewater. The system consumes about 15-16.3kWh per ton of water evaporated, which is much more energy-efficient than the system developed by the Heated steam-driven single-stage evaporation systems are 25 to 50 times lower.
In 2004, AGV Technologies Inc. of the United States of America considered other MVR technology based on a combination of We have developed a new MVR water treatment system called the membrane scraping rotating disc system, which is based on our own technology. The system has a rotating disc instead of a conventional heat transfer surface, which improves the heat transfer efficiency and reduces the generation of fouling. The size of the system has been scaled up, with heat transfer coefficients of up to 25 kW-M-2 – °C-1.
In addition to the major institutions mentioned above, in Europe GIG Karasek in Austria, EVATHERM in Switzerland. Germany’s MAN Diesel & Turbo, for example, has also carried out application research and promotion of MVR water treatment technology. Some countries in the Middle East are engaged in research on the application of MVR technology in the field of seawater desalination. It can be seen that MVR technology has received widespread attention in the field of water treatment from foreign countries, and has been continuously recognized and applied, especially in seawater desalination. field. According to statistics, MVR technology holds about 33% of the share of thermal separation systems in the world.
Since 2007, MVR technology has been introduced to the Chinese market from North America and Europe, and is mainly used in the food processing, dairy industry. In addition, the technology has been widely used in industries such as industrial wastewater treatment and beverages. Meanwhile, universities and research institutes in China are continuously conducting pioneering research on this technology. MVR has been studied in theory and practice by the Institute of Physics and Chemistry of the Chinese Academy of Sciences, the Beijing University of Technology, the Beijing University of Aeronautics and Astronautics, and others. Since 2008, with the increasing call for environmental protection and energy conservation, MVRs have been on the rise, and are used in a large number of applications and business Practice.